Steel and corrosion
Steel and corrosion
Main research interests:

Crack body during the grouting process
Steel and corrosion
In reinforced concrete construction, the durability of structural elements is essentially limited by two damage mechanisms - the electrochemical oxygen corrosion of steel and load-related material fatigue. The active anodic sub-process of corrosion can quickly lead to high material removal in concrete steels - accompanied by significant cross-sectional losses - which can endanger stability and, in extreme cases, lead to component failure. The investigation of electrochemical corrosion processes has been a research focus of ibac for decades. Numerous investigation methods, measuring equipment and test setups are available for this purpose, coupled with many years of experience, which means that both standardised investigations and individually developed test programmes can be carried out.
Various testing facilities are also available at ibac for the investigation of fatigue phenomena. Both the testing of the dynamic (cyclic) stressability of test specimens via the determination of the fatigue strength and investigations into the material behaviour under permanent loads are carried out regularly. The current subject of research is the combined effect of fatigue loads on corrosion-damaged steels. For this purpose, the currently most powerful large load resonance testing machine in the world with 1.5 MN amplitude is currently being procured for the investigation of the fatigue behaviour of reinforced concrete composite test specimens. Funding is provided by the DFG's "Large-scale equipment of the Länder" programme and is currently underway.
Corrosion of steel in concrete
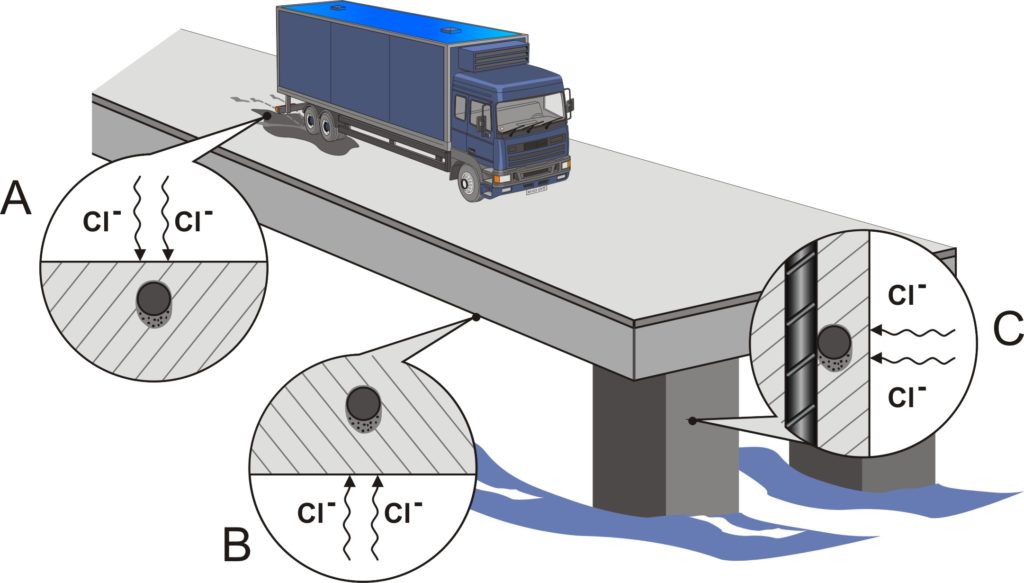
Chloride attack with different orientations in relation to concreting direction and reinforcement position
Critical corrosion-causing chloride content
Chloride-induced corrosion of steel in concrete is still one of the main reasons for the limited durability of reinforced concrete components. The so-called critical (corrosion-inducing) chloride content is of great importance here. Therefore, current research work is aimed at identifying the decisive influencing variables of this characteristic value. Particular attention is being paid to the influence of the contact zone between reinforcing steel and concrete as well as the practical design of test procedures.
Corrosion behaviour of the reinforcement in the area of cracks
Currently, the question of the corrosion behaviour of the reinforcement in separation cracks of multi-storey car park decks is controversially discussed in Germany in connection with various repair methods. In general, high cross-sectional losses of the reinforcing steel can quickly occur in separation cracks due to the direct chloride effect on the reinforcing steel in the crack area and the unfavourable surface ratios between anode and cathode, so that the stability is directly endangered. The recently completed research activities at ibac deal with the corrosion behaviour in separation cracks after short-term exposure to chloride over a winter period - before and after crack treatment by complete grouting with polyurethane under laboratory conditions. The results show a strong decrease in corrosion rates to a technically tolerable level. The transferability to practical construction conditions, under which complete crack filling is difficult to achieve, must be investigated in detail in the future.
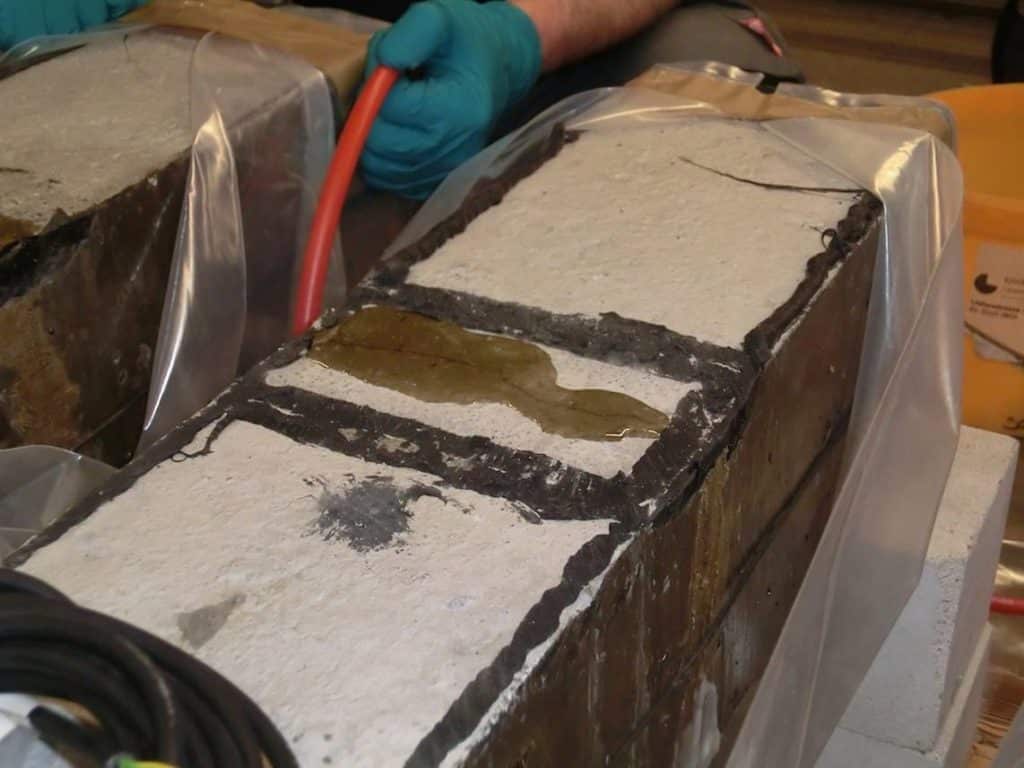
Crack body during the grouting process
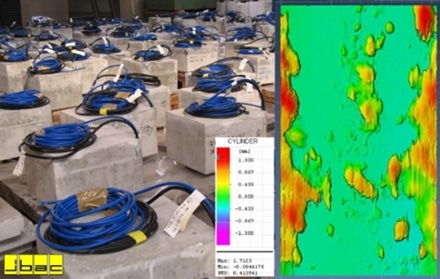
Chloride attack with different orientations in relation to concreting direction and reinforcement position
Time-dependent behaviour of anodic regions
The aim of the research is to model the active chloride-induced corrosion phase in chloride-induced corrosion of steel in concrete. Based on 8 test series with a total of 120 test specimens, the influence of specific boundary conditions on the temporal development of free corrosion potentials, polarisation resistances as well as selected geometric characteristic values of the anodically active partial areas is investigated over a period of several years. For the first time, a new method based on optical triangulation with structured strip light was used to evaluate the corrosion damage. This allows precise three-dimensional models of the damaged steel samples to be digitised and evaluated by computer.
Simulation of corrosion processes
In research projects dealing with the corrosion of steel in concrete, small-format laboratory test specimens are usually used to investigate the relevant parameters, since for reasons of reproducibility they have to be produced, stored and investigated in large numbers under conditions that are as identical as possible in order to take into account the given heterogeneity of the building material. However, important parameters influencing the corrosion process, such as the geometry of the reinforcement or the concrete cover, can usually not or only insufficiently be reproduced in the test. Here, numerical simulation has proven to be a valuable tool for transferring laboratory results to component geometries relevant to construction practice.
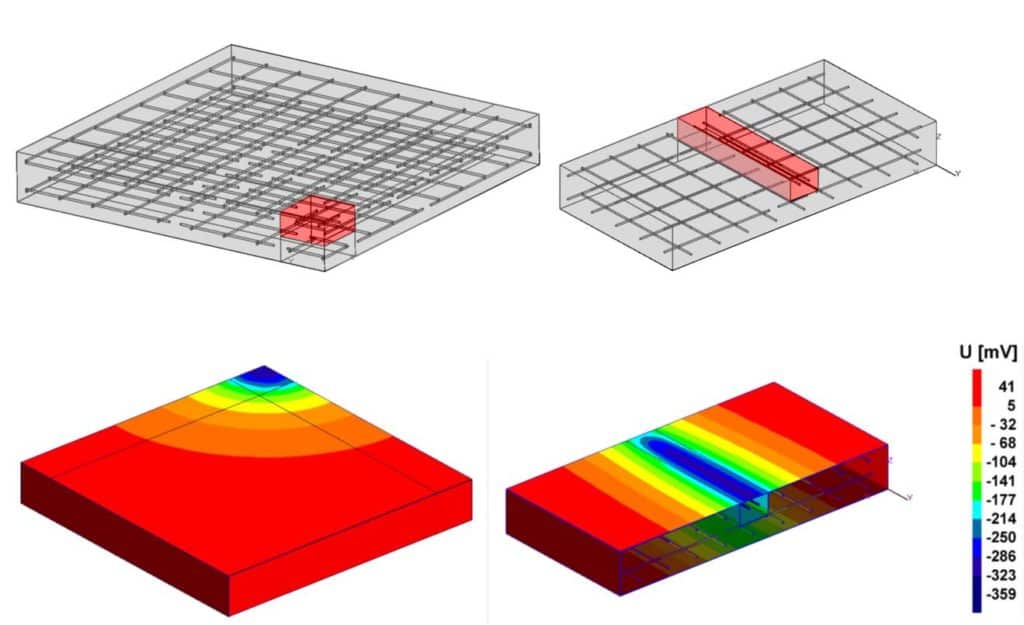
Numerical models (top) and potential distribution (bottom) of reinforcement geometries with point (left) and line (right) chloride contamination.
Influence of component geometry on macro-element corrosion
The research work aims to investigate the influence of geometric boundary conditions on the resulting macro-element flow in chloride-induced corrosion of steel in concrete. The investigations are not carried out exclusively by laboratory tests, but also by numerical simulations. The laboratory test specimens cover geometries relevant to practice and serve to verify the model calculations. Not only are measured and calculated macro-element currents compared, but also the respective polarisations of the individual electrodes. Based on this, numerical parameter studies are carried out to investigate the influences of selected boundary parameters such as the electrolytic conductivity, the driving voltages or the cathode/anode surface ratio.